來源:射頻微組裝;作者:王濟(jì)乾
01 引言
本文轉(zhuǎn)發(fā)南京電子技術(shù)研究所的王濟(jì)乾等發(fā)表在《電子機(jī)械工程》上的“基于硅基異構(gòu)集成的BGA 互連可靠性研究”一文,文中針對有源相控陣?yán)走_(dá)組件微系統(tǒng)化的需求,提出一種基于硅基的垂直硅通孔(TSV)基板與AlN 高溫共燒陶瓷(HTCC)厚薄膜混合基板的高密度異質(zhì)異構(gòu)集成方案,基板間采用球形柵格陣列(BGA)實現(xiàn)互連。
在異構(gòu)集成組件中,互連結(jié)構(gòu)通常是薄弱處,在經(jīng)過溫度循環(huán)、振動等載荷后,互連結(jié)構(gòu)因熱、機(jī)械疲勞而斷裂是組件失效的主要原因之一。目前的研究工作主要集中在芯片焊點可靠性上,且通常球形柵格陣列(Ball Grid Array, BGA)焊點的高度、球徑和節(jié)距較大,對組件層級互連結(jié)構(gòu)的可靠性風(fēng)險認(rèn)識不足,同時難以實現(xiàn)高密度BGA 失效預(yù)測。
文中首先基于硅基TSV 基板與AlN HTCC 厚薄膜混合基板異構(gòu)集成架構(gòu)實現(xiàn)單個BGA 焊點的精確建模,采用Anand 本構(gòu)模型對錫鉛、無鉛焊料BGA在?55 ℃ ~ 85 ℃ 溫度循環(huán)載荷下的內(nèi)部應(yīng)力應(yīng)變分布情況進(jìn)行仿真分析,以仿真結(jié)果為基礎(chǔ)構(gòu)建高密度BGA 陣列簡化模型,并基于田口正交法分析了在溫度循環(huán)載荷下焊球高度、球徑和節(jié)距三個因素對BGA 應(yīng)力、應(yīng)變的影響權(quán)重,從而有針對性地對BGA陣列結(jié)構(gòu)參數(shù)進(jìn)行優(yōu)化。通過Coffin-Manson 公式對優(yōu)化前后的焊點壽命進(jìn)行了預(yù)測,并與最優(yōu)參數(shù)異構(gòu)集成樣件溫度循環(huán)載荷實驗結(jié)果進(jìn)行比較,驗證了BGA 陣列結(jié)構(gòu)參數(shù)優(yōu)化的有效性。
02集成架構(gòu)及模型設(shè)置
本文采用的異構(gòu)集成架構(gòu)如圖1(a)所示,上層采用硅基TSV 基板,利用其高密度布線能力、良好的導(dǎo)熱能力以及與各類芯片良好的熱匹配,實現(xiàn)多種不同制程、材料芯片的高密度異構(gòu)集成。芯片的高密度引腳通過TSV 基板上表面重布線層(RDL)扇出后,通過TSV 向下引出至BGA。為實現(xiàn)高密度垂直互連,本文采用激光植球工藝在硅基TSV 基板背面預(yù)植BGA 焊球。該工藝最低支持球徑/節(jié)距為0.05 mm 且兼容Sn-Ag-Cu、Sn-Pb 等多種焊料體系的BGA 焊球預(yù)植。預(yù)植的BGA 焊球與AlN HTCC 基板通過薄膜工藝制備的表層RDL相連。相比于微波印制板、有機(jī)封裝基板等傳統(tǒng)封裝基板,在布線密度相當(dāng)?shù)臈l件下,AlN HTCC厚薄膜基板具有更強(qiáng)的抗彎折能力、更高的散熱系數(shù)以及與硅基TSV基板相近的熱膨脹系數(shù),因此該異構(gòu)集成架構(gòu)更適用于高集成密度、高可靠性的雷達(dá)組件。
1)仿真模型簡化
單個BGA 互連結(jié)構(gòu)的精確仿真模型如圖1(b)所示,從上至下分別為構(gòu)成硅基TSV 基板的Si-SiO2、BGA焊球及上下兩側(cè)RDL 金屬膜層體系以及底部AlN HTCC,盡管已經(jīng)略去了與BGA焊點關(guān)聯(lián)性不高的兩種基板內(nèi)部互連結(jié)構(gòu),但仍然存在十余種不同材料的結(jié)構(gòu),且相互之間尺寸差異巨大。AlN HTCC厚度為2.3mm,而作為粘附阻擋層的Ti厚度僅為50nm,相差46倍。為防止結(jié)構(gòu)尺寸的巨大差異導(dǎo)致仿真結(jié)果不收斂,需對模型進(jìn)行合理簡化。去除SiO2及兩側(cè)RDL金屬膜層體系后的簡化模型如圖1(c)所示。
2)Anand 本構(gòu)模型仿真
在室溫下,本文采用的Pb63Sn37焊點和SAC305焊點的歸一化溫度均超過了0.5,其在組件工作狀態(tài)下的主要應(yīng)變形式為粘塑性應(yīng)變,因此通過Anand本構(gòu)關(guān)系來計算兩種模型下材料的等效粘塑性應(yīng)變,以等效粘塑性應(yīng)變的大小及分布來驗證模型的簡化是否合理。仿真涉及的材料參數(shù)及兩種焊點材料的Anand本構(gòu)關(guān)系詳細(xì)參數(shù)見表1和表2。仿真中BGA焊球的高度和球徑分別設(shè)置為100μm 和200μm。
本文施加的溫度載荷如圖2 所示。溫度循環(huán)載荷的最低、最高溫分別為?55℃ 和85℃,從最低溫轉(zhuǎn)換到最高溫的時間為5min,轉(zhuǎn)換完成后在最低/最高溫度處保持30min,單個循環(huán)的時間為70min。焊點材料的應(yīng)力應(yīng)變遲滯環(huán)一般在3~4 個溫度循環(huán)載荷后保持穩(wěn)定,因而本文將6 個循環(huán)后焊點等效粘塑性應(yīng)變的分布和最大值作為模型簡化是否合理的評判標(biāo)準(zhǔn)。仿真結(jié)果如圖3 所示。
等效粘塑性應(yīng)變的分布一致且最大值均位于焊點與硅基TSV 基板(精確模型中為RDL 金屬膜層,簡化模型中為基板)的界面邊緣。精確模型Pb63Sn37和SAC305 焊點的等效粘塑性應(yīng)變最大值分別為0.235 和0.329,簡化模型Pb63Sn37 和SAC305 焊點的等效粘塑性應(yīng)變最大值則分別為0.281 和0.394,簡化模型的數(shù)值稍大于精確模型。這是由于兩種焊點材料的熱膨脹系數(shù)與RDL 金屬膜層更相近,而與兩種基板材料相差甚遠(yuǎn)。值得注意的是,焊點的疲勞壽命與其在溫度循環(huán)載荷下產(chǎn)生的等效粘塑性應(yīng)變成反比,基于簡化模型的可靠性分析更為嚴(yán)苛,因此本文采用簡化模型仿真是可行的。
03BGA結(jié)構(gòu)參數(shù)優(yōu)化及疲勞壽命預(yù)測
基于上一節(jié)的簡化模型,開展整個異構(gòu)集成架構(gòu)在溫度循環(huán)載荷下BGA的等效粘塑性應(yīng)變分析,并以其為優(yōu)化目標(biāo),通過田口正交法分析BGA 的球高、球徑和節(jié)距三個因素對等效粘塑性應(yīng)變影響的權(quán)重,從而有針對性地進(jìn)行參數(shù)優(yōu)化,以減小整體結(jié)構(gòu)的等效粘塑性應(yīng)變,提高系統(tǒng)的整體可靠性。模型整體由20mm×20mm×0.2mm 的硅基TSV基板,球高100μm、球徑200μm、節(jié)距200μm的40×40的BGA 陣列以及20mm×20mm×0.8mm 的AlN HTCC 基板構(gòu)成。本封裝架構(gòu)成軸對稱,因此在運(yùn)算資源有限的情況下,為確保運(yùn)算的準(zhǔn)確性,本文取整個結(jié)構(gòu)的1/4,并在BGA 焊球與基板相接的界面附近采用細(xì)化網(wǎng)格,從而實現(xiàn)大模型下更準(zhǔn)確的等效粘塑性應(yīng)變分析。1/4仿真模型及網(wǎng)格剖分如圖4 所示,標(biāo)藍(lán)界面采用了對稱邊界條件。
1)關(guān)鍵焊點定位
在溫度循環(huán)載荷下,由于焊點材料與基板材料的熱失配,所有焊點均發(fā)生粘塑性形變,但各焊點粘塑性形變的量不同,而BGA 失效首先發(fā)生在粘塑性形變累積最大的關(guān)鍵焊點處。本文首先基于上述1/4 結(jié)構(gòu)和Anand本構(gòu)模型對關(guān)鍵焊點進(jìn)行定位,再對球高100μm、球徑200μm、節(jié)距250μm 的BGA加載圖2所示的溫度循環(huán)載荷,仿真結(jié)果如圖5所示。
在6 個循環(huán)后,位于頂角處的焊點積累的等效粘塑性應(yīng)變比中心位置焊點相應(yīng)值大一倍以上。此焊點為整個集成架構(gòu)中最先失效的焊點,因此為關(guān)鍵焊點。
2)田口正交法結(jié)構(gòu)參數(shù)優(yōu)化
以關(guān)鍵焊點的等效粘塑性應(yīng)變?yōu)閮?yōu)化目標(biāo),基于Pb63Sn37 BGA 焊球的球高、球徑以及節(jié)距形成3因素3水平表(表3)。
按照田口正交法生成3因素3水平表格, 保持1/4 模型硅基TSV 基板尺寸( 10mm×10mm×0.2 mm)、AlN HTCC基板尺寸(10mm×10mm×0.8mm)及BGA陣列(20×20)不變,依據(jù)相應(yīng)的結(jié)構(gòu)參數(shù)進(jìn)行仿真并提取關(guān)鍵焊點的等效粘塑性應(yīng)變ep,得到表4 中的9 組數(shù)據(jù)。通過計算各結(jié)構(gòu)參數(shù)在不同水平下等效粘塑性應(yīng)變的累加值K1、K2、K3 及其極差R,得到結(jié)構(gòu)參數(shù)影響權(quán)重次序為球徑>球高>節(jié)距,BGA 的最佳結(jié)構(gòu)參數(shù)為球高60μm、球徑200μm及節(jié)距250μm。相比于初始條件(BGA球高100μm、球徑200μm 及節(jié)距250μm) , 優(yōu)化結(jié)構(gòu)參數(shù)后BGA 在6 循環(huán)載荷后積累的等效粘塑性應(yīng)變由0.256下降至0.163,下降了57.06%,相較于等效粘塑性應(yīng)變累積最大的結(jié)構(gòu)參數(shù)(BGA 球高100μm、球徑120μm 及節(jié)距150μm)下降了167.48%。
3)優(yōu)化前后焊點疲勞壽命對比
本文討論的焊點在溫度循環(huán)載荷下主要發(fā)生粘塑性應(yīng)變,適宜的疲勞壽命預(yù)測公式為Coffin-Mason 方程。該方程描述了材料低周疲勞壽命Nf 和粘塑性應(yīng)變范圍ep 之間的關(guān)系:
式中: 為疲勞韌性系數(shù); 為材料的疲勞韌性指數(shù)。
針對導(dǎo)致焊點失效的多種因素,大量學(xué)者不斷對Coffin-Mason 方程進(jìn)行了修正,其中針對熱循環(huán)載荷和循環(huán)載荷頻率的修正方程為:
對于等效粘塑性應(yīng)變累積最大的結(jié)構(gòu)參數(shù)(球高100μm、球徑120μm、節(jié)距150μm) 、初始結(jié)構(gòu)參數(shù)(球高100μm、球徑200μm、節(jié)距250μm)以及優(yōu)化后的結(jié)構(gòu)參數(shù)(球高60μm、球徑200μm、節(jié)距250 μm),經(jīng)過6 個溫度循環(huán)載荷的等效粘塑性應(yīng)變積累曲線如圖6 所示。
由圖6 可知,在3 個循環(huán)后,等效粘塑性應(yīng)變的增量趨于常數(shù),提取的第6 個循環(huán)的等效粘塑性應(yīng)變范圍Δep 分別為0.036、0.022 和0.014,將該數(shù)值帶入式(2),得到優(yōu)化前后焊點的疲勞壽命分別為182次循環(huán)、626次循環(huán)和1953次循環(huán)。結(jié)構(gòu)參數(shù)優(yōu)化后焊點的疲勞壽命較等效粘塑性應(yīng)變累積最大的結(jié)構(gòu)參數(shù)及初始結(jié)構(gòu)參數(shù)分別提升了973.07% 和208.86%。
04基于優(yōu)化結(jié)構(gòu)參數(shù)的樣件實驗與討論
為進(jìn)一步驗證有限元仿真的結(jié)果,本文選用優(yōu)化后的結(jié)構(gòu)參數(shù)( 球高60μm、球徑200μm、節(jié)距250μm)制備實驗樣件,施加圖2 所示的溫度循環(huán)載荷,并觀察其失效模式。
1)AlN HTCC 厚薄膜混合基板制備
為匹配上述兩種結(jié)構(gòu)參數(shù)的BGA,在10 層AlN HTCC 基板表面進(jìn)行減薄拋光,實現(xiàn)平面度和粗糙度的優(yōu)化,再通過前處理、金屬層濺射、光刻、電鍍、蝕刻等薄膜工藝[9]制備直徑為100μm、節(jié)距為170μm的焊盤陣列及直徑為180μm、節(jié)距為270μm 的焊盤陣列。前者匹配球徑為120μm、節(jié)距為150μm 的BGA陣列,后者匹配直徑為200μm、節(jié)距為250μm的BGA 陣列。焊盤表面膜層為Ti(50 nm)-Cu (2 μm)-Ni (3 μm)-Au (300 nm),為40 × 40 陣列,與前文所述模型一致,如圖7 所示。
2)準(zhǔn)同步激光植球
本文通過準(zhǔn)同步激光植球工藝在兩種AlNHTCC 厚薄膜混合基板表面分別預(yù)植了具有高一致性的Pb63Sn37 BGA 焊球,使硅基轉(zhuǎn)接板與預(yù)植焊球的AlN HTCC 厚薄膜混合基板對準(zhǔn),并通過調(diào)整回流焊參數(shù),使焊球塌陷至接近仿真中的參數(shù)(球高100μm、球徑120μm、節(jié)距150μm 及球高60μm、球徑200μm、節(jié)距250μm),從而實現(xiàn)硅基TSV基板與AlN HTCC 厚薄膜混合基板的異構(gòu)集成,如圖8 所示。
3)溫度循環(huán)載荷試驗
采用圖2 所示的溫度循環(huán)載荷,在兩件樣品分別進(jìn)行500 次循環(huán)后,對樣品邊緣的關(guān)鍵焊點進(jìn)行剖樣,得到兩件樣品的焊點形貌,如圖9 和圖10 所示。
對于等效粘塑性應(yīng)變累積最大的結(jié)構(gòu)參數(shù)樣品(球高100μm、球徑120μm、節(jié)距150μm),施加的循環(huán)次數(shù)遠(yuǎn)大于其計算出的失效循環(huán)次數(shù),位于樣品邊緣關(guān)鍵焊點處的BGA 焊球已與焊盤完全脫開,互連完全失效;而對于結(jié)構(gòu)參數(shù)優(yōu)化后的樣品,不論是在仿真中展示的最大粘塑性形變積累處( 焊球與RDL 金屬膜層體系相接處)還是在BGA 剖面中的其他部位,均未發(fā)現(xiàn)明顯的失效裂紋及空洞。該結(jié)果與仿真結(jié)果相互印證,證實BGA 焊點結(jié)構(gòu)參數(shù)優(yōu)化有利于大幅提升焊點的可靠性。
-
封裝
+關(guān)注
關(guān)注
128文章
8685瀏覽量
145493 -
BGA
+關(guān)注
關(guān)注
5文章
573瀏覽量
48684 -
基板
+關(guān)注
關(guān)注
2文章
305瀏覽量
23523 -
異構(gòu)集成
+關(guān)注
關(guān)注
0文章
39瀏覽量
2085
原文標(biāo)題:基于硅基異構(gòu)集成的BGA 互連可靠性研究
文章出處:【微信號:深圳市賽姆烯金科技有限公司,微信公眾號:深圳市賽姆烯金科技有限公司】歡迎添加關(guān)注!文章轉(zhuǎn)載請注明出處。
發(fā)布評論請先 登錄
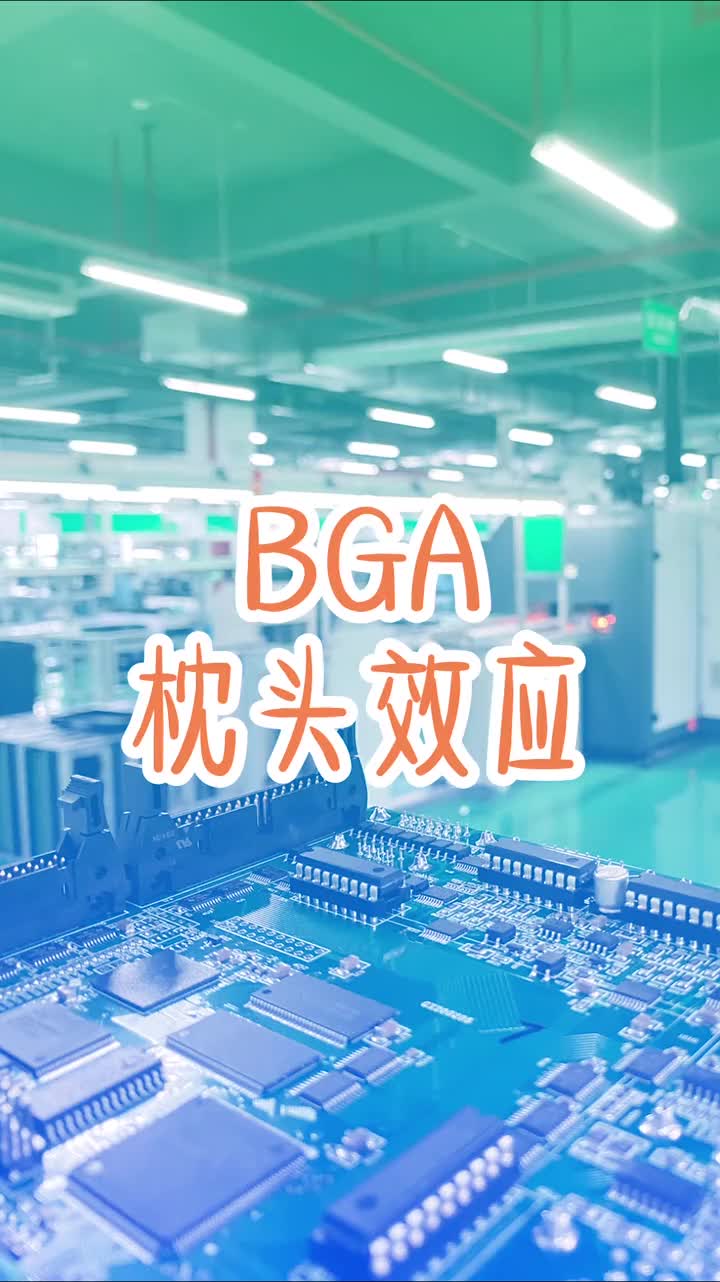
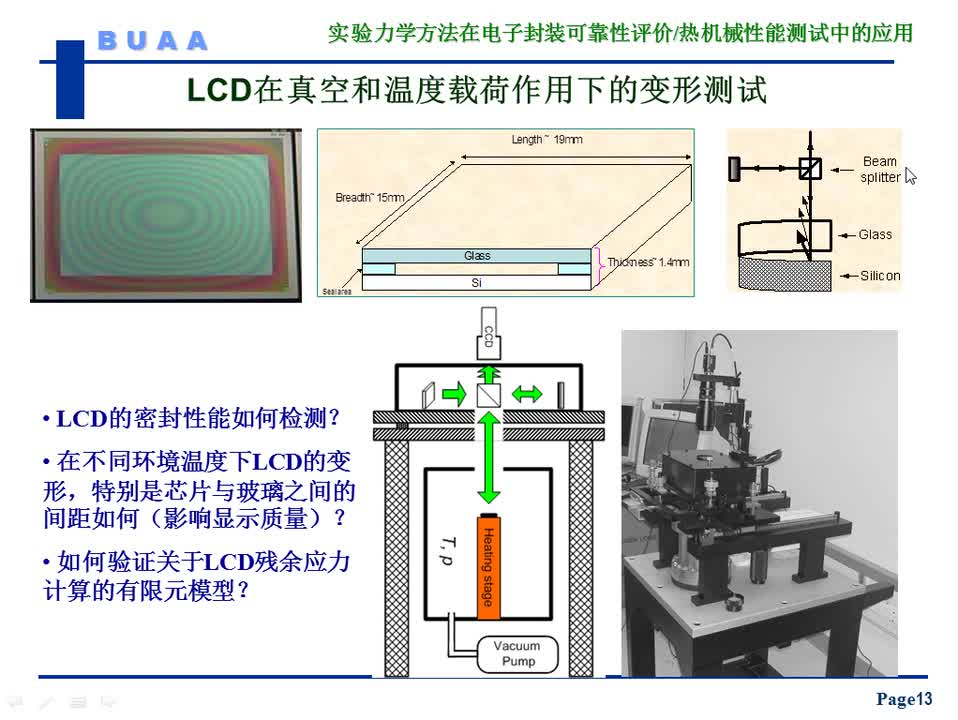
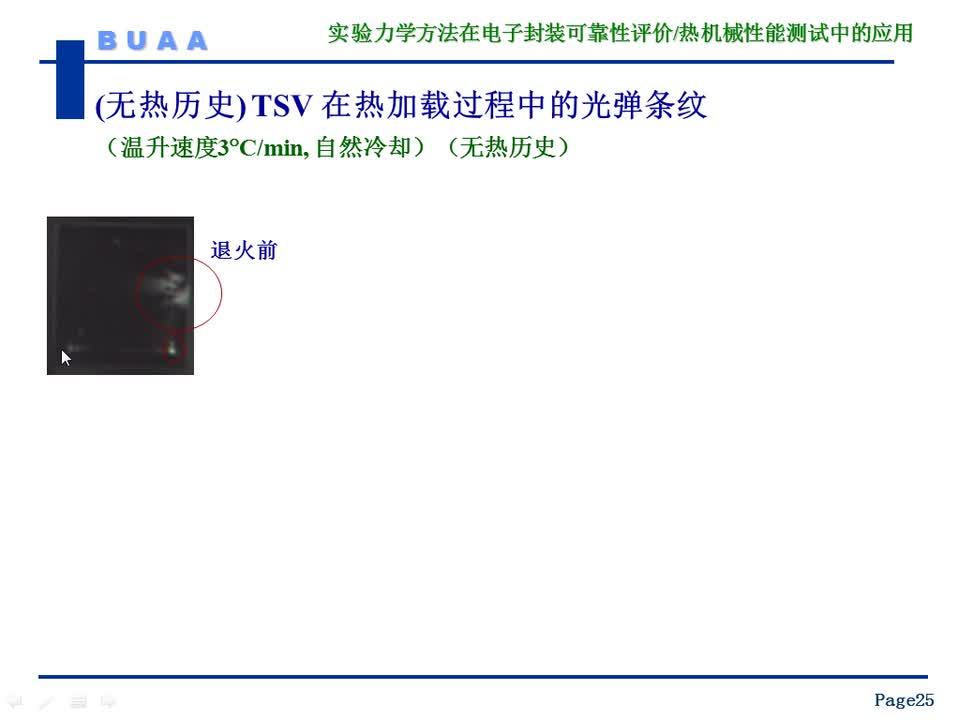
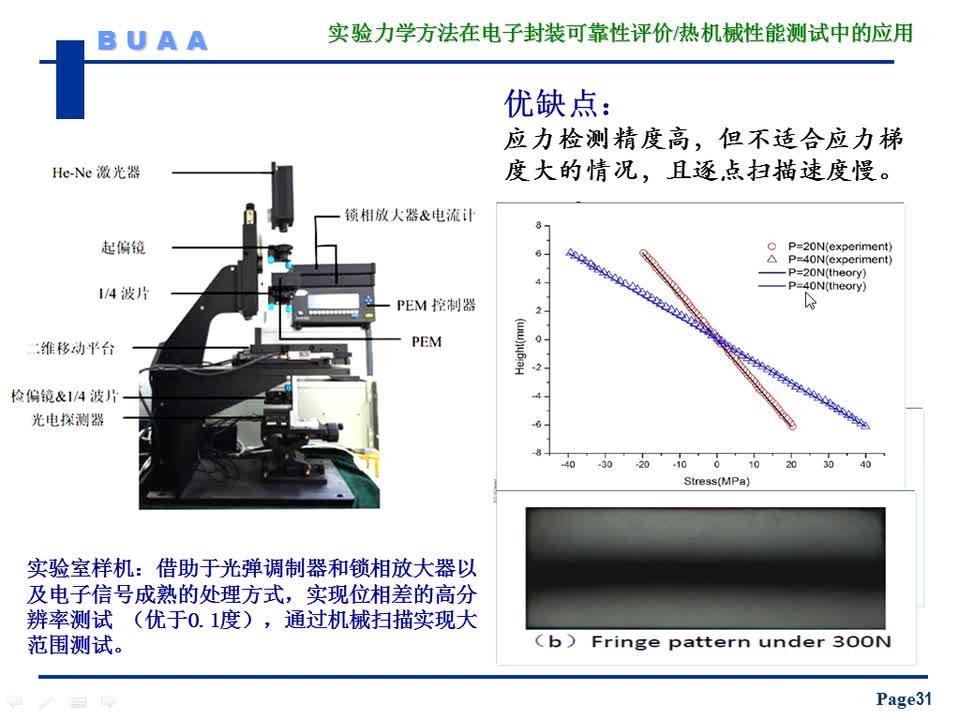
基于Multisim 10的電子電路可靠性研究
無鉛焊接互連可靠性的取決因素
硅壓力傳感器的可靠性強(qiáng)化試驗
BGA焊接工藝及可靠性分析
單片機(jī)應(yīng)用系統(tǒng)的可靠性與可靠性設(shè)計
BGA封裝的PCB布線可靠性
BGA焊接可靠性評價指引方案
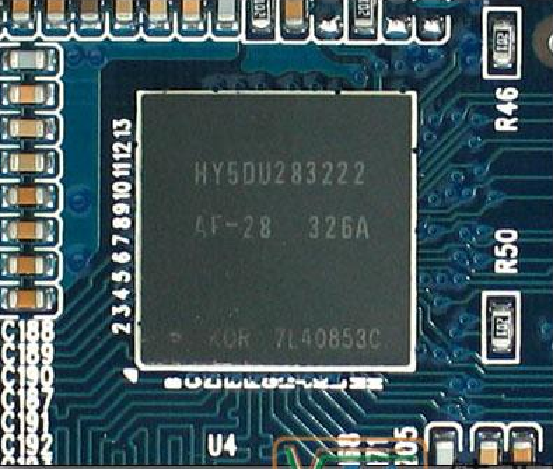
硅基異質(zhì)集成工藝的簡介
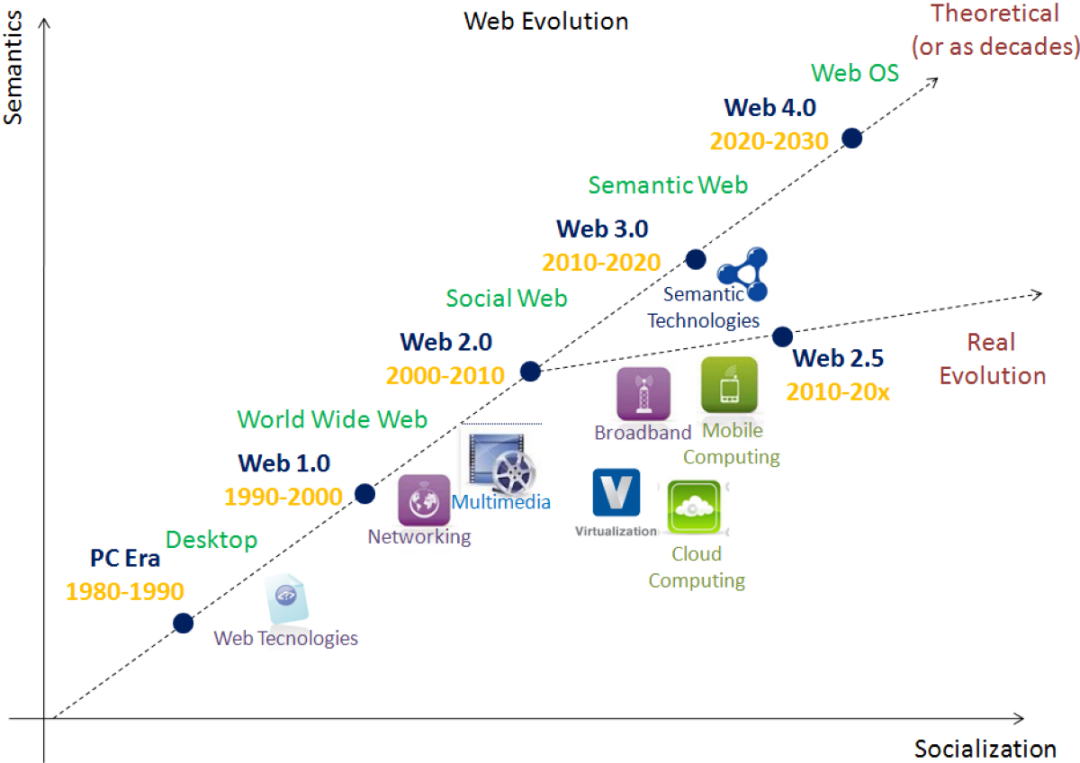
硅通孔技術(shù)可靠性技術(shù)概述
BGA封裝焊球推力測試解析:評估焊點可靠性的原理與實操指南
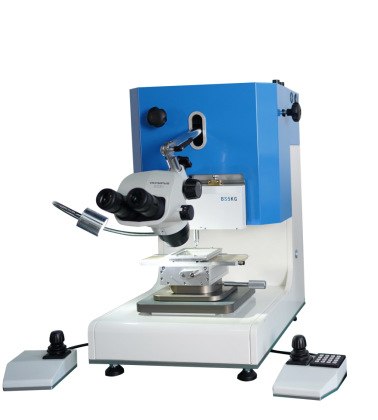
評論